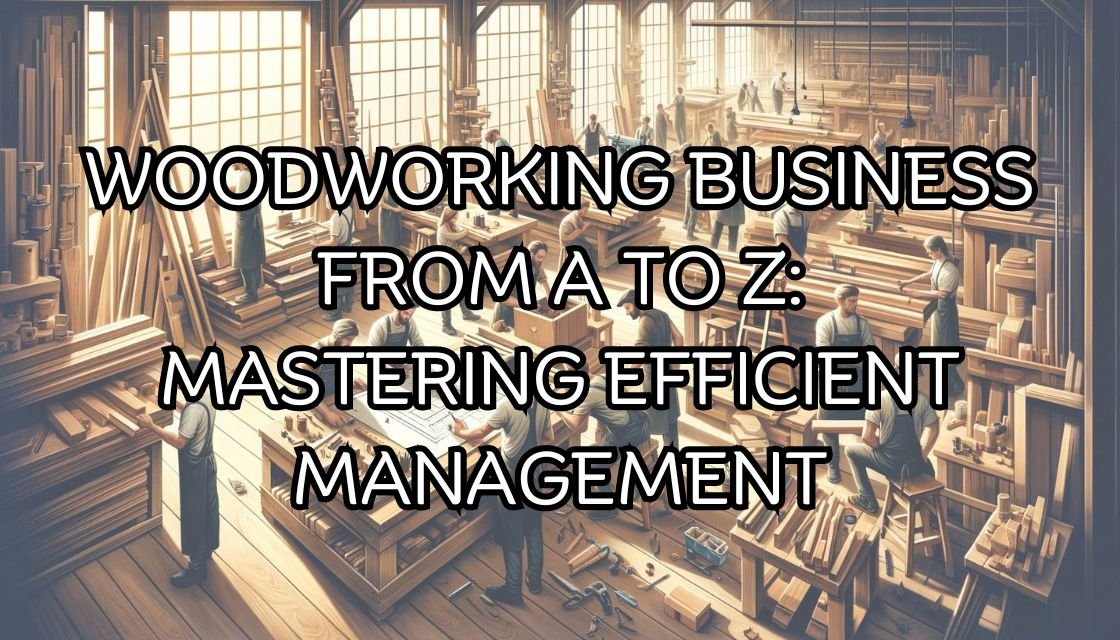
In the whirlwind of modern industry, the woodworking sector stands out as both an art and a science, a blend of traditional craftsmanship with modern efficiency. For anyone at the helm of a woodworking business, the journey from raw timber to polished product is fraught with challenges and opportunities. The key to success? Efficiency. But how can you ensure that every cog in your woodworking machine runs smoothly? That’s where we come in. Let’s dive deep into the heart of efficient woodworking business management, from A to Z.
Introduction
The woodworking industry, with its rich heritage and modern innovations, is a dynamic field that combines the charm of natural materials with the precision of contemporary manufacturing. In this competitive landscape, efficiency isn’t just a buzzword; it’s the backbone of profitability and sustainability. But how do you transform challenges into stepping stones towards success? The secret lies in understanding your operations, setting clear goals, and optimizing every facet of your factory’s workflow.
Part I: Setting the Stage for Success
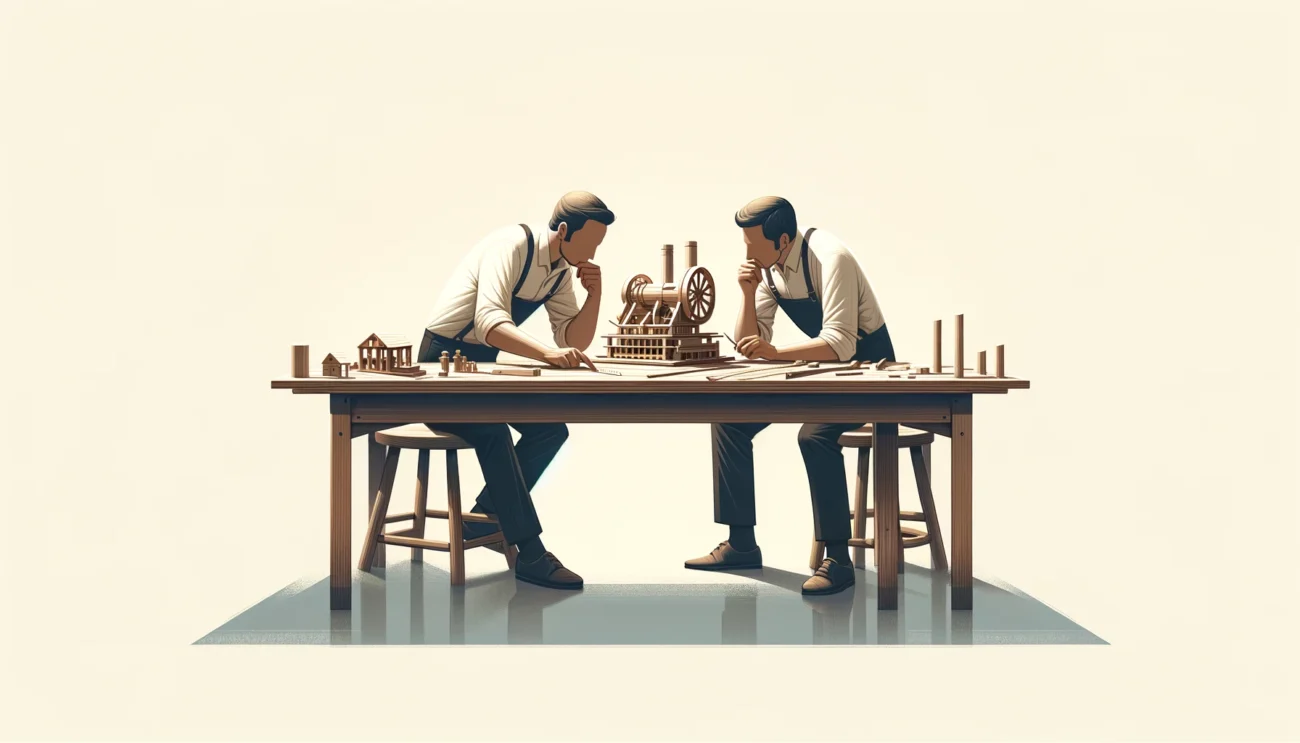
A. Understanding Your Business
Before you can run, you need to walk — and that means taking a comprehensive look at what your woodworking business does, how it operates, and what it aims to achieve. Core Operations of a woodworking business are varied, ranging from sourcing raw materials to the final finishing touches on your products. Each step requires precision, care, and a keen eye for detail.
Moving on to Products and Services: What Are You Offering? Every piece of wood has a story, and as a manufacturer, you’re the one telling it. Whether you specialize in bespoke furniture, intricate joinery, or mass-produced wooden items, understanding your product line inside and out is crucial. It’s not just about what you make; it’s about the value you bring to your customers.
B. Goals and Objectives
Setting the right Goals and Objectives is like plotting a course through uncharted waters. Where do you see your business in the next year, five years, or decade? Establishing Clear, Achievable Goals is the first step toward turning your vision into reality. These goals should be specific, measurable, attainable, relevant, and time-bound (SMART).
Understanding the difference between Long-term vs Short-term Objectives is also vital. Short-term objectives keep your factory running day-to-day, while long-term goals focus on growth, innovation, and sustainability. Balancing the two is the dance of successful management.
Part II: Operations Management
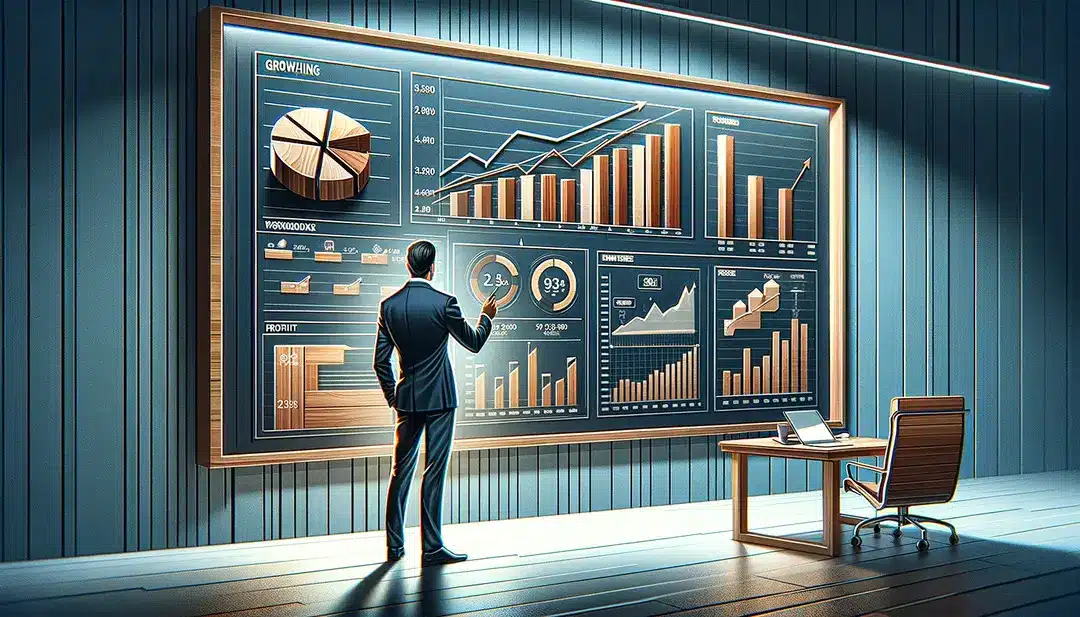
A. Raw Material Sourcing and Storage
In the world of woodworking, the journey of every product begins with the right raw material. Identifying Reliable Suppliers is not just about finding the best price; it’s about ensuring quality, sustainability, and reliability. Building strong relationships with suppliers means you’re never left in the lurch when it comes to stocking up on high-quality wood.
Once you’ve got your materials, Storage Solutions for Different Types of Wood become paramount. Different species of wood have varying needs in terms of humidity, temperature, and storage position. Implementing an organized and effective storage system minimizes waste and keeps your raw materials in top condition.
B. Production Processes
Overview of Woodworking Processes: From cutting and shaping to joining and finishing, each step in the woodworking process requires specific tools, techniques, and attention to detail. Streamlining these processes through lean manufacturing principles can significantly boost efficiency without compromising on the artisanal quality of the final product.
Optimizing Workflow for Efficiency involves meticulously planning your production layout, minimizing movement, and reducing bottlenecks. It’s about creating a symphony where every movement is purposeful and every task is optimized for speed and quality.
C. Quality Control Measures
No matter how efficient your processes, quality is the linchpin that holds everything together. Implementing Standard Operating Procedures (SOPs) ensures that every piece produced meets a set standard of excellence. These SOPs should cover everything from material selection to final inspection.
Tools and Techniques for Ensuring Product Quality might include everything from traditional craftsmanship techniques to modern technology like CNC machines and laser cutters. Regular training and upskilling of your workforce are also crucial in maintaining high-quality standards.
D. Maintenance and Upkeep
The heart of any woodworking business is its machinery and tools. Regular Maintenance Schedule for Machinery ensures that your equipment runs smoothly and efficiently, minimizing downtime and costly repairs. It’s not just about fixing things when they break; it’s about preventing issues before they arise.
Handling Repairs and Downtimes Effectively is also key. Even with the best maintenance plan, things can go wrong. Having a swift, efficient system for repairs and a contingency plan for downtimes ensures that your production is back on track as quickly as possible.
Part III: Workforce Management
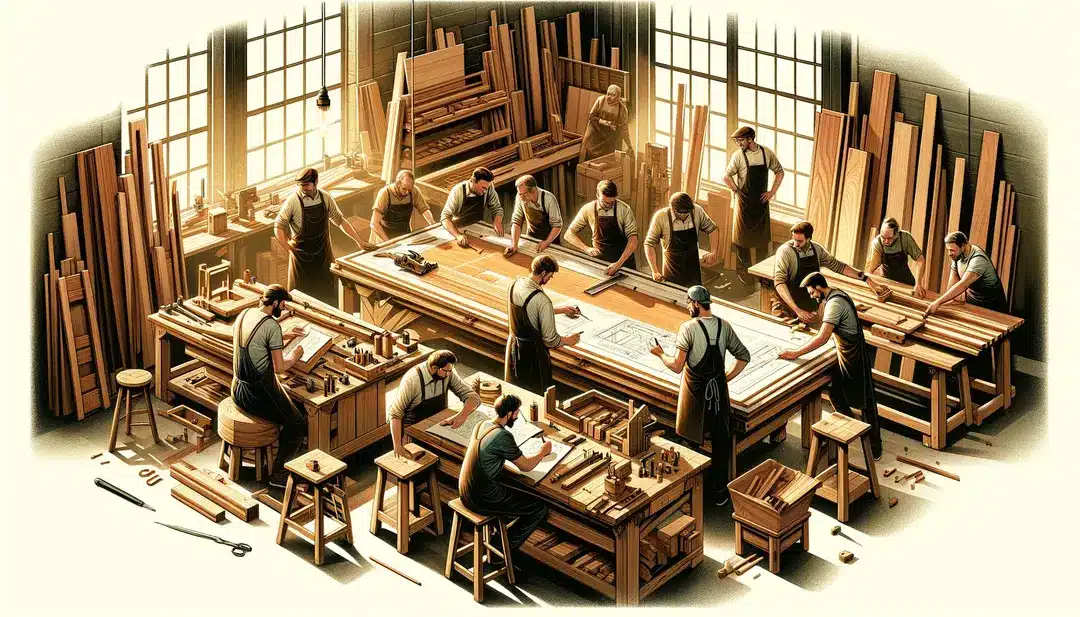
A. Building Your Team
Your team is your most valuable asset. Hiring Skilled Workers and Specialists who share your passion for woodworking is just the start. Creating a culture of learning, innovation, and respect is what keeps those skilled workers with you for the long haul.
Training Programs for Skill Enhancement not only improve the quality of your products but also empower your employees, making them feel valued and part of something bigger. Investing in your team’s growth is investing in the future of your woodworking business.
B. Safety and Well-being
In an industry where the work can be physically demanding and the environment filled with potential hazards, Ensuring a Safe Working Environment is non-negotiable. Adherence to health and safety regulations is just the starting point; fostering a culture where safety is everyone’s responsibility is the goal.
Health and Safety Regulations Compliance protects not just your employees but also your business. Regular safety drills, up-to-date equipment, and clear, accessible information on safety practices are all pillars of a safe workspace.
C. Performance and Motivation
Keeping your team motivated and performing at their best is both an art and a science. Performance Evaluation Methods should be fair, transparent, and constructive, focusing on growth and development rather than merely pointing out shortcomings.
Strategies to Motivate Your Team can range from tangible rewards like bonuses and promotions to intangible ones like recognition, autonomy, and opportunities for professional growth. Remember, a motivated team is an efficient team.
Part IV: Technological Integration
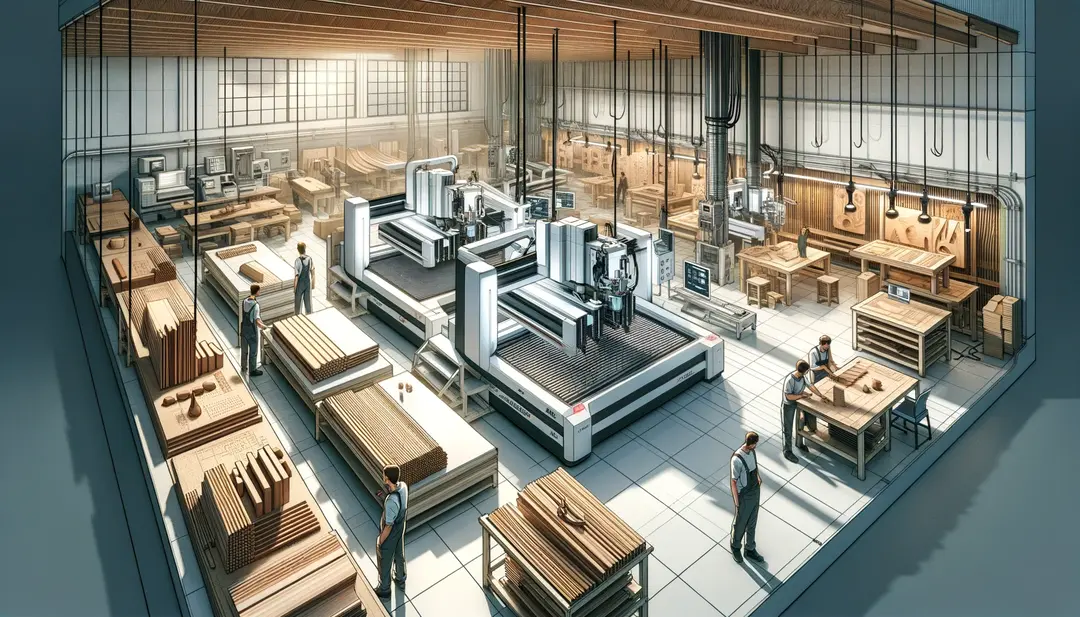
A. Adopting Modern Technologies
In today’s digital age, The Role of Automation and Robotics in woodworking cannot be overstated. From CNC routers that cut intricate designs with precision to automated sanding and finishing lines that ensure consistent quality, technology can significantly enhance productivity. Embracing these advancements doesn’t mean replacing human craftsmanship; it means augmenting it, allowing for more creativity and efficiency.
Software Solutions for Inventory and Sales Management are equally crucial. Imagine having real-time data on your stock levels, orders, and customer preferences at your fingertips. This not only streamlines your operations but also provides invaluable insights for making informed business decisions.
B. Data and Analytics
Using Data for Strategic Decision Making transforms raw numbers into actionable insights. Whether it’s tracking production metrics, analyzing sales trends, or forecasting demand, data analytics can give you a competitive edge by helping you make decisions based on facts, not just gut feelings.
Tools for Monitoring Efficiency and Productivity range from simple applications to comprehensive ERP systems. Implementing these tools can help identify bottlenecks in your processes, optimize resource allocation, and ultimately, drive your factory’s performance to new heights.
Part V: Financial Management
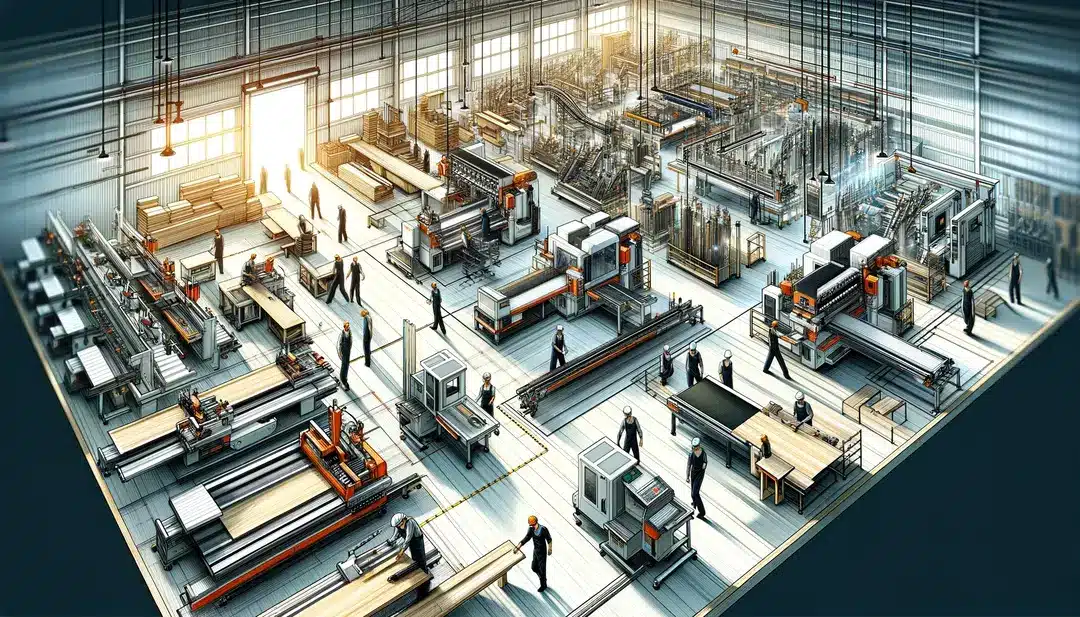
A. Budgeting and Cost Control
Planning Your Financials with precision is vital for the health and growth of your business. A detailed budget helps you anticipate future costs, manage cash flow, and allocate resources wisely. It’s about striking the right balance between cutting unnecessary expenses and investing in areas that will yield the highest returns.
Techniques for Cost Reduction and Control might involve negotiating better rates with suppliers, improving energy efficiency, or reducing waste. Remember, every dollar saved in costs directly boosts your bottom line.
B. Profit Maximization Strategies
In the quest for profitability, Pricing Strategies for Your Products play a critical role. Setting prices too high might deter customers, while prices too low can erode your profit margins. The key is understanding your market, your costs, and your value proposition to price your products strategically.
Expanding Revenue Streams could mean diversifying your product line, exploring new markets, or offering value-added services like custom design consultations. The goal is to not just rely on a single source of income but to build a robust, diversified revenue model.
Part VI: Marketing and Sales
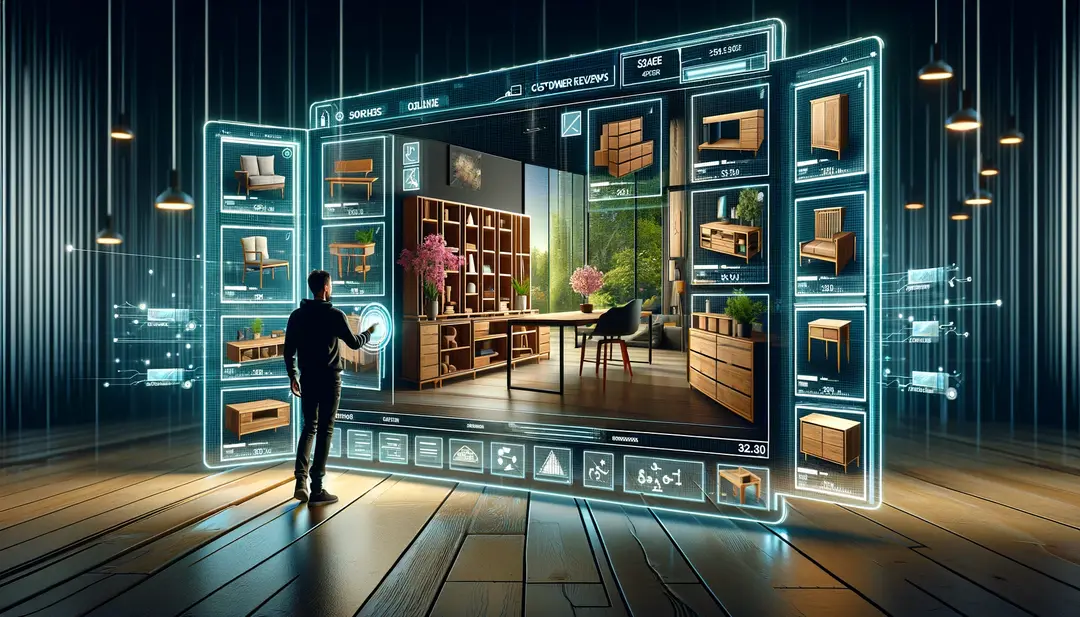
A. Branding and Market Positioning
Developing a Strong Brand Identity is essential in distinguishing your woodworking business from the competition. Your brand should reflect the quality, craftsmanship, and uniqueness of your products, creating an emotional connection with your customers.
Target Market Analysis and Positioning involves understanding who your ideal customers are, what they need, and how your products can meet those needs better than anyone else’s. Effective market positioning ensures that your marketing messages resonate with your target audience, driving sales and building loyalty.
B. Sales Channels and Distribution
In the digital era, Online vs Offline Sales Strategies must be carefully balanced. While an online presence can open up global markets, offline sales through showrooms or partnerships can provide customers with the tactile experience that’s so important when buying wood products.
Building a Distribution Network is about more than just logistics; it’s about building relationships with retailers, distributors, and even other manufacturers. A strong network can extend your reach, reduce shipping costs, and increase your products’ availability to end consumers.
Part VII: Sustainability and Growth
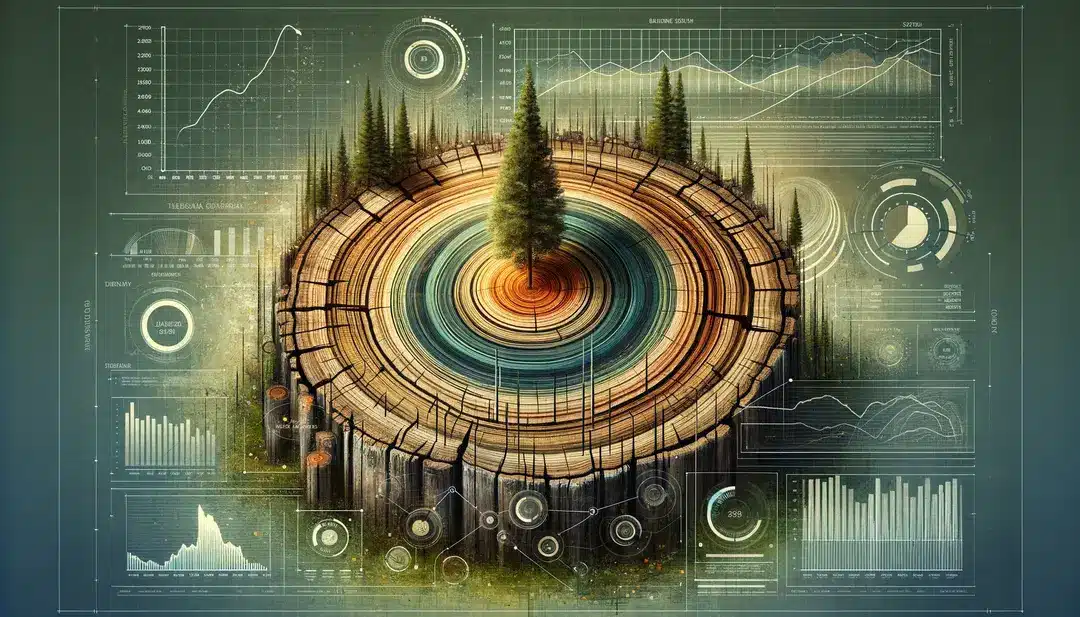
A. Sustainable Practices
In an industry that relies heavily on natural resources, Implementing Eco-friendly Manufacturing Processes is both a moral imperative and a competitive advantage. This could mean anything from using sustainably sourced wood to adopting manufacturing processes that reduce waste and energy consumption.
Waste Management and Recycling Initiatives not only help in minimizing environmental impact but also in reducing costs. Finding innovative uses for offcuts, sawdust, and other by-products can turn waste into a resource, contributing to both sustainability and profitability.
B. Scaling Your Business
Identifying Opportunities for Expansion requires a keen eye for market trends and an understanding of your factory’s capacity to grow. Whether it’s investing in new machinery, entering new markets, or acquiring smaller competitors, growth should be strategic and sustainable.
Partnerships and Collaborations for Growth can open up new avenues for business development. Collaborating with designers, architects, or even technology companies can enhance your product offering and expand your market reach, driving your factory’s growth to new heights.
Conclusion
Efficiently managing a woodworking business is a multifaceted challenge that requires a delicate balance between craftsmanship and innovation, tradition and technology. By understanding your business, optimizing operations, empowering your workforce, embracing technology, managing finances wisely, strategically marketing your products, and committing to sustainability, you can not only survive but thrive in the competitive landscape of the woodworking industry. The journey from A to Z in managing your woodworking business is complex, but with the right strategies and tools, it’s not just possible; it’s profoundly rewarding.
Frequently Asked Questions (FAQs)
-
u003cstrongu003eWhat are the most critical challenges in managing a woodworking business?u003c/strongu003e
Managing a woodworking business comes with numerous challenges, including maintaining quality while increasing efficiency, managing costs, sourcing sustainable materials, and navigating fluctuating market demands.
-
u003cstrongu003eHow can technology impact the efficiency of woodworking operations?u003c/strongu003e
Technology, from automation and robotics to software for inventory and sales management, can significantly enhance the efficiency of woodworking operations by streamlining processes, reducing waste, and providing actionable insights through data analytics.
-
u003cstrongu003eWhat strategies can be employed to keep the workforce motivated and productive?u003c/strongu003e
Strategies to keep the workforce motivated include offering competitive compensation, providing opportunities for training and development, recognizing and rewarding performance, and creating a safe and positive work environment.
-
u003cstrongu003eHow can a woodworking business become more sustainable?u003c/strongu003e
A woodworking business can become more sustainable by using sustainably sourced materials, implementing eco-friendly manufacturing processes, reducing waste through recycling initiatives, and optimizing energy use.
-
u003cstrongu003eWhat are the future trends in the woodworking industry?u003c/strongu003e
Future trends in the woodworking industry may include increased use of sustainable and recycled materials, greater integration of technology and automation, more personalized and customized products, and a continued focus on craftsmanship and quality.
Thank you for these lovely posts. On a note abour branding… why are you using American spelling for Jewellery and Glamour for what appears to be a london based site? It is confusing, and leaves English people suspicious. In the US, they view trinkets as jewels hence Jewelry, but in the UK we view trinkets as things made by those selling jewels, (called jewellers), hence their trinkets are jewellery.